As the world’s vehicle fleet decarbonizes by transitioning to electric drivetrains, the answer to what makes the best battery remains elusive.
Electric vehicle consumers seek a comfortable range from battery capacity as well as easy access to charging stations, especially those with fast-charging capabilities. Current lithium-ion batteries leave room for improvement in these areas and can present safety and weight concerns.
Electric vehicle battery fires are not common, but when they do occur the batteries’ chemistry makes them more difficult to extinguish than fires fueled by gasoline. In Texas, it took firefighters four hours to subdue the flames from a Tesla vehicle that ignited due to a crash, requiring between 25,000 and 30,000 gallons of water.
Lithium-ion batteries are also large and heavy, which can increase both the batteries’ size and their strain on road and parking infrastructure. Engineers in the U.K. have expressed concerns that old, improperly maintained parking structures could collapse under the weight of heavy electric vehicles as they become more common.
Candace Chan, an associate professor of materials science and engineering in the Ira A. Fulton Schools of Engineering at Arizona State University, is working on two projects to help alleviate problems in applications that use lithium-ion batteries such as electric vehicles. Through these projects, she is investigating how to make solid-state batteries a viable solution for consumer applications.
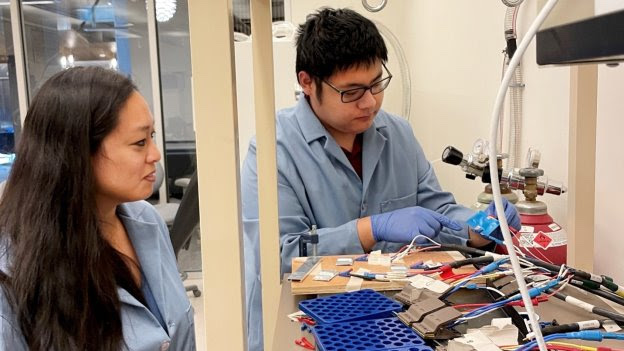
Setting solid-state battery technology on solid ground
Solid-state batteries differ from traditional battery chemistry due to the electrolytes used. An electrolyte is the material in a battery that transports ions between the cathode and the anode, which are also known as electrodes.
The cathode stores lithium ions when charged, which then travel through the electrolyte to the anode and generate electricity in the process. The electricity is then delivered to the device the battery powers.
A standard lithium-ion battery design uses a liquid electrolyte, while solid-state batteries use an electrolyte made from solid material. Chan’s group focuses on solid electrolytes made from ceramic materials.
“These solid electrolytes should ideally have the same properties as the liquid electrolyte to allow lithium-ion transport, but much better safety properties due to their increased thermal stability,” says Chan, a faculty member in the School for Engineering of Matter, Transport and Energy, part of ASU’s Fulton Schools.
This increased stability in the electrolyte’s chemical structure also paves the way for potential use of lithium metal in the anode section of a battery. Doing so would increase the battery’s charging capacity, extending the driving range of electric vehicles.
Chan believes that using lithium metal for battery anodes could even make electric aircraft a possibility.
“Currently, lithium metal anodes cannot be used in lithium-ion batteries with liquid electrolytes,” she says. “This is because of the tendency of lithium metal filaments known as dendrites to grow inside the batteries, through the liquid electrolyte, and cause internal short circuits. The hope is that solid-state electrolytes can prevent dendrite formation and allow for the realization of these higher-energy-density batteries.”
Building a better battery
Chan is participating in two projects pertaining to different aspects of solid-state batteries with Yoon Hwa and Nick Rolston, assistant professors of electrical engineering in the School of Electrical, Computer and Energy Engineering, part of ASU’s Fulton Schools.
The first project, funded by the National Science Foundation and led by Hwa, seeks to develop the best way to manufacture a solid-state lithium-sulfur battery. Lithium-sulfur battery chemistry has the potential for low-cost, safe and high-capacity energy storage.
However, the challenge lies in the design of the interfaces, or points of connection, between the battery’s electrodes and the electrolyte. Chan says it is difficult to find an interface design that allows the battery to work properly.
Chan and Hwa will experiment with different interface designs to find the best solution to transport power through the battery for storage and later use. They will examine how the size, structure and integration of various cathode and solid electrolyte materials influence performance.
Aniruddha Deb, an associate research scientist at the University of Michigan, will bring his expertise in chemistry to the project by introducing synchrotron X-ray analysis — a method to view the electrochemical processes taking place inside the batteries as well as changes in internal structure as the batteries are charged and discharged.
“Our systematic approach, which incorporates material synthesis and robust characterization techniques, aims to provide insightful feedback on solid-state interface design strategies,” Hwa says. “This will catalyze a technological breakthrough in the field, setting the stage for the production of high-performance lithium-sulfur solid-state batteries.”
Manufacturing efficient solid-state batteries
Chan’s second project, also funded by the NSF and conducted in collaboration with Rolston, researches commercially viable manufacturing methods for solid-state batteries.
Current manufacturing methods for solid-state battery electrolytes use furnaces that take 12 hours to create material that is very brittle.
“I’ve taken tweezers, poked at the material and it broke apart,” Rolston says.
This fragility means solid-state battery electrolyte layers need to be thick to effectively bind the material together. But the slow process is not cost-effective for commercial applications, hindering the uptake of solid-state batteries for consumer use.
Chan and Rolston are investigating a faster process that takes less than 12 minutes, creates thinner, more durable material and doesn’t require a sealed chamber. The furnace is replaced with an open-air plasma device that uses high amounts of energy to convert and treat materials.
Typically, this plasma treatment is used in solar panel manufacturing, but Chan and Rolston are investigating similar methods for solid-state batteries.
Rolston says if the process works, it could create batteries that have a useful life of 10 years, or three times that of current lithium-ion designs. He adds that the technology is still in its early stages and will take time to perfect.
“We still have to understand the materials better to make sure that we’re producing these in the right forms and control the defects and the way they’re made and scaled up,” he says. “You develop something in the lab; but then, if you want to make electric vehicle batteries, you had better be making millions of them. That introduces additional challenges.”
New equipment aids ASU’s battery research
Chan’s research is aided by new equipment at ASU, much of it funded through the Advanced Materials, Processes and Energy Devices Science and Technology Center, or AMPED STC. The AMPED STC is boosting research, innovation and entrepreneurship in the areas of photovoltaics, batteries and power electronics.
The investment will allow ASU to build a battery research and development facility for fabricating electrodes and assembling batteries. Among the equipment are new tools that allow researchers to conduct failure analysis of batteries or look at what’s happening inside a battery during or after its charge and discharge cycles.
One example is an X-ray diffractometer that ASU acquired using more than $550,000 in funding from the NSF’s Major Research Instrumentation Program, in addition to university funds. This tool enables structural measurements of the battery materials as they simulate a variety of conditions, such as atmosphere type, temperature and electrical bias.
Chan and her research team plan to use the instrument to measure batteries’ operating parameters during their charge and discharge cycles, furthering their knowledge beyond what was previously capable at ASU.
With new tools and new research, Chan sees a future for commercialization of solid-state batteries. But it may be far off.
“It took several decades for the lithium-ion batteries we commonly use today to be commercialized after they were first developed, and even more decades for them to be widely used in applications such as consumer electronics and electric vehicles,” she says. “There is still a lot of work to be done to understand how to make solid-state batteries with the performance, reliability and commercial volumes that lithium-ion batteries currently enjoy.”
Read more Technology articles on Green Living.