BY SHELBY TUTTLE
Patagonia, a leader in sustainable outdoor gear, has taken a significant step towards circularity in the wetsuit industry. This innovation comes through a collaboration with Bolder Industries, a company specializing in sustainable solutions for the rubber and plastics sectors.
Patagonia’s commitment to eco-friendly materials began in 2008 with its partnership with Yulex. This collaboration resulted in the development of bio- based rubber derived from Pará rubber tree sap, a significant departure from the traditional petroleum- based neoprene. This pioneering move not only reduced environmental impact but also ushered in a new era of sustainable wetsuit materials.
GIVING WETSUITS A SECOND LIFE
Recognizing the potential for further environmental benefits, Patagonia initiated a program to collect retired Yulex wetsuits. These decommissioned suits undergo a novel transformation at Bolder Industries. Through a groundbreaking process, Bolder breaks down the wetsuits at the molecular level, recovering valuable “carbon black.” This recovered carbon black plays a crucial role in dyeing the recycled nylon lining of future Yulex wetsuits.
“We hope that this breakthrough in recycling and circularity will go well beyond the surf industry and will eventually be implemented across countless product sectors,” says Hub Hubbard, Patagonia’s surf product line manager. “We have successfully piloted this program using reclaimed carbon black (RCB) from retired Yulex wetsuits as a main component in wetsuits and that cycle can repeat indefinitely.”
THE POTENTIAL OF RECLAIMED CARBON BLACK
Patagonia’s partner in the initiative, Bolder Industries, has expertise that also extends beyond wetsuits. Its technology allows the company to reclaim carbon black from end-of-life tires (ELTs), resulting in a new technology called BolderBlack — an environmentally responsible alternative to virgin carbon black. The company’s BolderBlack technology produces a staggering 90% reduction in both water usage and greenhouse gas emissions. Bolder mixes recovered carbon black from wetsuits with ELT-derived black to ensure sufficient volume for each new wetsuit.
The recovered carbon black constitutes 10-20% of the rubber content in Patagonia’s latest wetsuit iteration. This achievement demonstrates a commitment to not only minimizing environmental impact but also continuously improving existing processes.
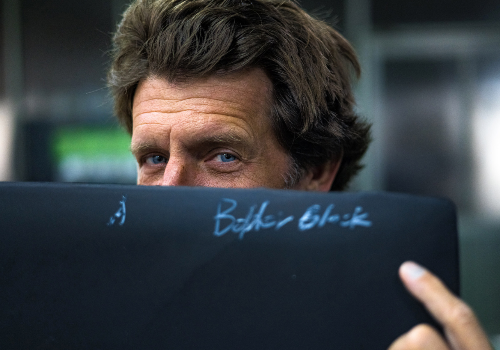
Mackenzie Warner, a Patagonia material developer, says, “While collaborating on this material with Bolder Industries, we discovered that recovered carbon black from rubber scraps and Yulex wetsuits can be utilized to not only solution dye wetsuit materials but also black fabrics and trims to make products such as packs and jackets.”
Patagonia’s Wetsuit Forge, a dedicated research, development, and repair facility, serves as the collection point for end-of- life wetsuits. Here, zippers are removed before the suits are shipped to Bolder Industries for carbon black extraction. The reclaimed material is then forwarded to Patagonia’s manufacturing partner, Sheico, for the production of the new, more sustainable wetsuits.
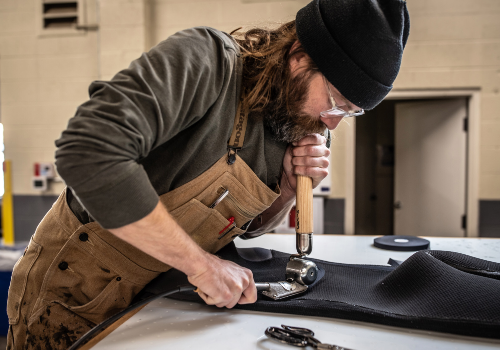
The first wave of wetsuits utilizing this groundbreaking recovered carbon black technology is expected to hit the market in 2025. This development signifies a significant advancement in wetsuit sustainability, paving the way for a more circular future within the industry.